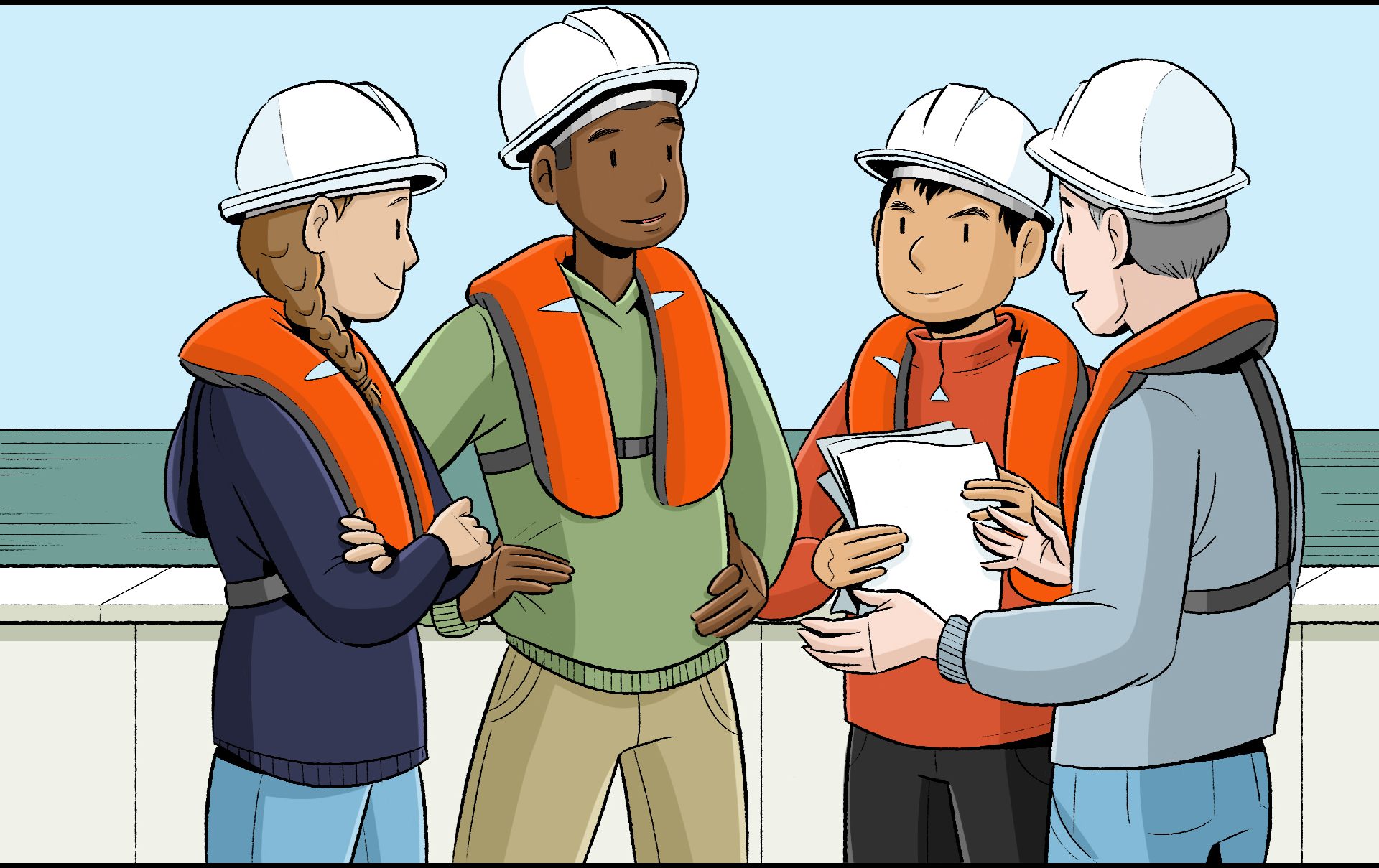
Alvin Forster, Loss Prevention Executive at Sunderland Marine, looks at the importance of toolbox talks.
Everyone is probably aware of the old adages when it comes to planning.
The favorite’s are usually the five P’s (‘Proper Planning Prevents Poor Performance’ – feel free to slip in the extra ‘P’ before ‘Poor’!) and a variation of US ex-President Benjamin Franklin’s “If you fail to plan, you are planning to fail”.
Clearly, preparing for what is ahead so that everyone knows what to expect and what they are supposed to do makes common sense. If people are prepared and know their roles, then it can go a long way towards preventing incidents that lead to injuries, and ultimately claims.
‘Work planning’ can conjure up images of meetings and charts. But planning doesn’t always have to be a lengthy or complicated process. One of the most simple and quickest methods can be one of the most effective; and it is probably the most overlooked – the ‘toolbox talk’.
It’s good to talk
A toolbox talk is an open and informal discussion just before starting a job. It helps make sure everyone involved knows what is going to happen and what they have to do.
Before the reader switches off, it’s important to know what a toolbox talk isn’t. It is not a training session, a lecture or another exercise in paperwork. A good and effective toolbox talk will be quick (no more than a few minutes), to-the-point and interactive.
Here are some tips to make your toolbox talks effective:
- Discuss the job – how it is going to be done and what is everyone’s role.
- Consider the impact of any other work being carried out on board or ashore.
- The person in charge can lead but don’t let it become a lecture. Get everyone involved as they can share their experience.
- No waffling or straying off-topic: Keep to the point, as toolbox talks work best when they are relevant and concise
- Talk about the risks and explain how they will be managed.
- If there is a written procedure or risk assessment relevant to the task at hand, run through them and check that they are correct, up-to-date and workable.
- If there are new crew on board, it is even more important to make sure they understand what is going on.
- Remember, things change – it is a dynamic working environment so discuss what to do if something isn’t right or circumstances change.
If your toolbox talk highlights a problem with a procedure or risk assessment, don’t ignore it. Investigate it and put it right.
At the end of the talk, everyone should know and understand what is to be done, how they are going to do it and what is their role. If everyone understands the risks and the reasons for the instructions, they are more likely to follow them.
For more details – Click here to download our quick-reference guide on toolbox talks.
Alvin Forster
Loss Prevention Executive (Sunderland Marine)